品質って何?
品質が悪いのは、
製品設計が悪いから、製造設備が悪いから、部品が悪いから、作業者が悪いから、・・・
不良率が0%でないから、品質は悪いの?
それは、本当?
不良率やクレームを”0(ゼロ)”にはできません。
人、モノ、設備、しくみの出来具合の総和が不良率なのです。
不良率(悪いところ)だけに目を向けて、付加価値は上がりますか?
事業が成長しない限り、新たな投資はできないのです。
褒めて伸ばすの如く、品質マネージメントシステムはパラダイムシフトしています。それが、ISO9001 2015年版なのです。
今からこそ、正の循環を起こして、事業に貢献する品質マネージメントシステムに変革しましょう。
筆者の極論ですが、
発生した不良は、放っておいても良いのです。
不良は、工程中の検査やスクリーニングが機能している証拠です。
”いい加減の不良率”なら原因追及は、二の次でもいいのかもしれません。
むしろ、
正の循環からすると、例えば、不良率10%の場合、それを見込んで生産性を10%向上させることが本来の取組とすべきです。
具体的な事例を示せば、HONDAのCABが日本生産に切り替えたとたん、人気が上がり、今では3〜6カ月待ちです。
ここでは、日本生産の商品であるとする潜在的品質(価値)が評価されているのです。CAB自体の評価は受けていないのです。だって、誰も手にしていないので^^;
熊本HONDAはこの状況に対して、何をしたのでしょうか?納期を延ばしたのです。しかも、納期確約もしていないのです。
でも、ユーザは、計り知れない期待(品質)を評価し、じっと待っています。
要するに、納期遅れということを品質問題にせず、時間軸の改善を行って、ユーザの期待(商品品質)に応えたのです。
とはいえ、やはり不良に目を向けた取組も必要です。
そのために、可視化を図り、事業にマイナスの要素(設定したKPI)となる場合に”改善”の取組をすべきです。
「品質改善で、新たな検査工程を追加しました。」
これって、新たな付加価値を生みますか?単に、設備費が増えて、作業工数が増える。つまりは、固定費を上げるだけです。
当然ながら、損益分岐点も上がり、利益を下げるだけです。
生産性を向上させることに着目すれば、固定費はそのままに、変動費(材料費)を上げる仕掛けです。実はここに量の理論が起きるのです。
要は、材料単価の引き下げ機会となるのです。
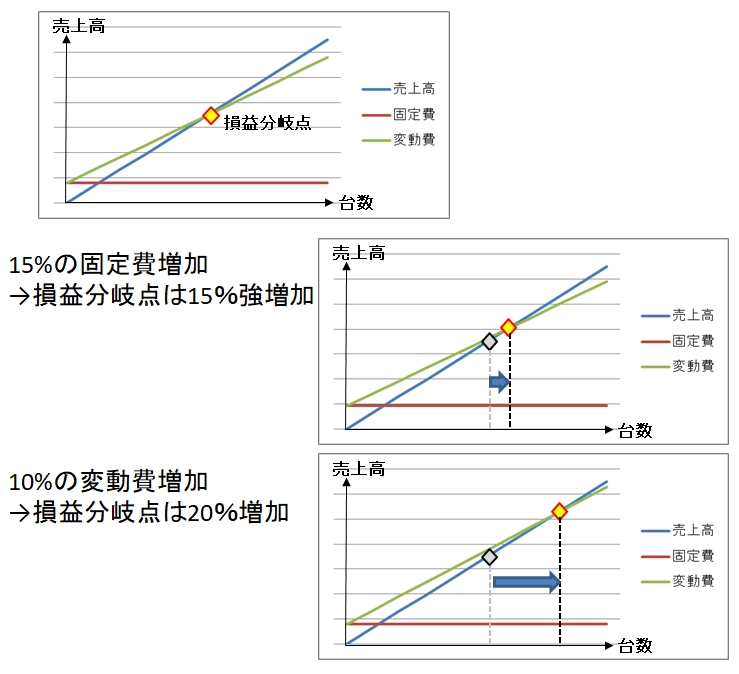
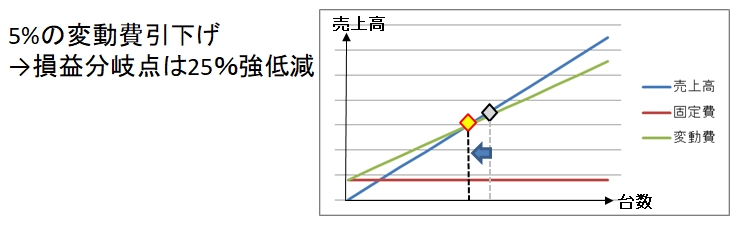
前述に戻ると、設備投資することは、フリーキャッシュを使うことで、新たな事業機会を失うことになるのではないでしょうか?
これらが、BSシート経営、キャッシュフロー経営と言われている理論です。
理論と述べましたが、これが、日頃の改善活動の本質です。
「品質とコストのトレードオフ」という言葉が象徴的ですね。
この「Q Manager」では、「品質状況の可視化」を行うサイトです。
現時点では、悪さ加減の情報と思われがちですが、
ここからの気づきで、「正の情報可視化」を狙っています。
狙いのデータ
・直行率
・納期遵守率
・部品棚卸資産
(T2)